
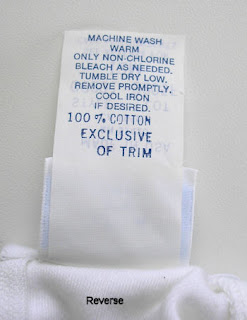
The first thing that caught my eye was the placement of the country of origin. Country of origin information must be placed so that it can be seen without flipping the label over. Nothing can cover the country of origin information, like a brand label. It should be placed in an easily accessible area, like the back neck or waistband.
Another interesting observation is the style number and lot number information included on the front of the label. The lot number probably refers to the production lot and corresponds to a date of manufacture (lot numbers are unique to each company, so it could mean almost anything). Generally, this information is found elsewhere, like the reverse of the tag or even on a separate tag stuck into a side seam. It is certainly not anything that a customer is going to care about. I like the inclusion of this info for easy back-tracking, but it should be placed elsewhere.
This tag contains both an RN and CA numbers. The CA number is the Canadian equivalent to the the US RN number. This product was most likely sold in both Canada and the US, thus the need for two numbers.
The reverse side of the label contains all relevant information. My only nit-pick is the overall formatting. I generally prefer the content information first, followed by the care info. This label is just the opposite. Further, the content information is a different font, font size, and right-aligned compared to the care instructions. It makes the whole reverse side appear sloppy.
My final nit-pick is that the label should say "2 piece set" somewhere. Inevitably, the two pieces will be separated. This helps the shipping and store employees on the retail end realize there should be two pieces on the hanger.