I admit that sometimes I make mistakes. A person reading my previous blog entry on a wedding care/content label pointed out some inaccuracies in how I wrote my suggested label. The FTC has some guidelines on how to write labels, both for content and care. I've read these instructions many times, but I sometimes need a refresher. Yes, it would be a good idea for anyone who has to write labels to read the instructions themselves rather than rely on a blog entry (or an anonymous commenter).*
Care instructions follow the general form:
Washing
Bleaching
Drying
Ironing
Warnings
If a dress truly cannot be dry cleaned, then the label should include that instruction. My label suggestion would be more accurate if I had included that instruction. I had also placed the bleaching instruction in the wrong order. Perhaps a better, more accurate, and perhaps correct label (changes in bold) would read:
100% Polyester
Do not dry clean.
Hand wash or
Spot clean in cold
water with mild
soap. Do not bleach.
Hang to dry.
Do not iron.
Made in China
RN12345 (<------ Made up)
---------------------
Avoid the use of
alcohol based products
such as hairspray,
perfume, etc., as these
may damage the dress.
The commenter also pointed out that if there is a reasonable basis for care instructions, then a manufacturer does not need to destroy a dress to prove it. I guess the question that must be determined is what is reasonable? In my opinion (and just for this commenter, this IS my opinion, for what it's worth), a new wedding dress manufacturer should destroy a few dresses to prove their labels. If you think something can be dry cleaned, you should be able to prove it. Same with any other care instructions. Over time, you may be able to reduce the type and amount of testing provided you do not change your component parts. This is probably the reason behind some of the testing requirements in the CPSIA. When you change a component (sometimes even from the same source), you have introduced a variable which may result in different testing guidelines.
I know wedding dresses are expensive, even the initial samples. Is it reasonable that every dress be tested to prove the care instructions? I am not sure every manufacturer goes to that extreme. But it is reasonable that a few have been. Testing a whole complete unit is the only way to test for compatibility of components. Testing a whole complete unit will tell you what a customer will experience. Wedding dresses have a lot of sentimental value and you wouldn't want a customer to have a dress ruined by poor or incorrect cleaning instructions. But this decision is best left to the manufacturer and the responsibility they are willing to bear if something were to go wrong.
As a manufacturer develops, it is reasonable to also test components. It is common for a manufacturer to use the same polyester satin in multiple styles and all they do is change up the trimming. In this case, the satin has probably been washed tested a few times and they know how it should be cleaned. But the trimming is different. In this case, I take some yardage, stitch the trim on and wash it (or dry clean it) - multiple times.
I can recall some concern I had about some flocked glitter on a chiffon. The glitter can fall off because the dry cleaning solvents will dissolve the glue. Washing by hand or machine can cause the glitter to fall off due to abrasion. So we tested various scenarios and came up with a reasonable basis for care. The same scenario can be applied to beads. Though I must say, based on my experience testing, some beads can be dry cleaned and some cannot. Some will fall apart even when hand washing. You won't know unless you test.
It is reasonable that a manufacturer has proof for the testing they recommend. I believe this includes documentation. You won't have documentation unless you test something. These days, I am not sure that a government regulator will appreciate your good intentions or your word without some kind of proof.
And finally, it is true that the CPSIA does not specifically mention wash testing (as I stated in my previous blog entry). It does imply that any testing be done by a certified 3rd party lab. When I worked various private label programs for Big Box stores, they required wash testing by an approved 3rd party testing lab. At that time we were able to negotiate creating an in-house wash testing program to save money. We were required to submit a copy of our test results with the 3rd party testing reports to the technical designers of the big box stores. In the days of CPSIA, I imagine this is no longer possible (I haven't worked on any private label programs in a while, so someone else who has will have to clarify this point). So while the law may not specifically mention wash testing by a certified lab, Big Box retailers might require it anyway. This is thus my reasoning for why I said what I said.
*When I wrote my original blog entry, the FTC site was down and had been down for a few weeks. My intention was to verify and correct my article and I didn't do that because I couldn't. It was one of those things that fell off my radar and I didn't get back to it. My apologies to anyone if I misled. I appreciate comments that politely correct me when I have misstated something. However, I won't print comments that are insulting and offensive.
Showing posts with label FTC. Show all posts
Showing posts with label FTC. Show all posts
February 04, 2010
August 12, 2009
A Warning on Labeling Bamboo Textiles
Bamboo fabric has long been considered a miracle green fabric. It is super soft, absorbent, biodegradable, and considered antimicrobial. It is true that bamboo is considered an eco friendly plant because it can be grown quickly without the use of chemicals. Many products have been produced from bamboo - from floors to textiles. Some of the eco friendly claims have come under scrutiny, especially bamboo textiles.
Bamboo textiles are produced by two methods. One can be considered sort of green and the other not. With the first method, bamboo stalks are crushed and broken down with enzymes and then combed out. The second utilizes harsh chemicals to break down the bamboo stalks into pulp which is extruded by spinnerets. This second method is the same process in which Rayon fabrics are manufactured.
You can bet that the majority of the bamboo fabrics on the market are manufactured by the second method. Because of this, the FTC has declared that bamboo fabrics must be labeled Rayon with the qualifier from bamboo. While this is a controversial position taken by the FTC, it is more accurate due to the actual processes being used. The FTC has clamped down on some companies claiming their bamboo textiles are "green". The charges include falsely advertising some of the more outlandish claims of being antimicrobial and biodegradable.
Anyway, be careful of how you label bamboo. The FTC has further guidance on how to deal with bamboo.
Labels:
Bamboo,
Care/Content Tags,
Eco Friendly,
Fabric,
FTC,
Labels,
Rayon,
Regulations,
Sustainable,
The Business End
July 07, 2009
Wedding Dress Care-Content Labeling

This article now has a follow-up blog entry with some corrections and additional opinions. Your comments are welcome, but hateful or spammy comments will be deleted.
As I was working on the alterations for this wedding dress, I wanted to see other dresses by this designer/maker. Perhaps the sleeve pattern shaping was intentional and not a mistake? Perhaps the problem is consistently found in other styles? I had no idea who the designer was, only where the dress was purchased. The dress was not in the store's web catalog and the only label in the dress was not helpful. The dress was missing a brand label and had no RN number. Further, the care instructions were rather bizarre/interesting (click on the picture for a closer view). I googled the style number and came up empty.
At a minimum, the dress should have had an RN number on the label. You can search an FTC database to find out the manufacturer of an apparel item. Wedding dress manufacturers/bridal shops have been fined in the past for failing to disclose or intentionally removing this information. Alterationists may remove the labels after purchase but should give them to the bride (links to come later as the FTC website was having problems when I wrote this).
The label states:
100% polyester
Do not dryclean
Spot clean ONLY
Use cold water and
mild soap
Made in China
See reverse for care
----------------------
Do not spray Alcohol
based product directly
on gown such as Perfume,
Hairspray....etc. This will
damage beadworks and
embroiderie designs made of
Rayon, Nylon, and other
synthetic materials.
I found the care instructions rather hilarious. How many of you spot cleaned your wedding dress with only cold water and mild soap? The fabrics themselves probably could be dry cleaned or even hand washed (though that may be more work). The beads will probably dissolve in the dry cleaning solvents, so thus the "do not dry clean" instructions. But, if you can find a reputable dry cleaner who will clean the dress and avoid the beads, then go ahead and have the dress dry cleaned. Otherwise, hand wash the dress. BTW, there were no further care instructions on the back of the label. Many wedding dresses are currently manufactured in China, which may explain the poorly written tag.
The extra instructions are interesting. I suppose it is possible that perfume or hairspray may damage the beads. Though the bride would probably need to be drenched in it before the beads dissolved. Sure would like to put those beads to the test....
The label should have been written to say:
100% Polyester
Hand wash or
Spot clean
in cold water with
mild soap. Hang to
dry. Do not bleach,
Do not iron.
Made in China
RN12345 ( ------ Made up)
---------------------
Avoid the use of
Alcohol based products
such as hairspray,
perfume, etc., as these
may damage the dress.
And of course, the care instructions should be thoroughly tested by the manufacturer. Good industry practice (and the government) dictate that a manufacturer should have a reasonable basis for the cleaning instructions. This means actual test data recorded and stored with the manufacturer. At this point in time, manufacturers (except children's clothing manufacturers) can do their own in-house wash testing. Children's clothing manufacturers will have to have it done by a certified laboratory. Wash testing is not specifically mentioned in the CPSIA, but it does imply that ANY testing will have to be done in a certified lab.
Labels:
Care/Content Tags,
Cleaning,
CPSC,
CPSIA,
Dry cleaning,
Fabric,
FTC,
Labels,
Testing,
Wash testing,
Wedding dress
April 10, 2007
Country of Origin labeling examples
One comment from a reader on my Designers hate care/content labeling blog made a good point. Labels can be very irritating to the end user. Rest assured, it is perfectly legal to remove labels after purchase. The size and placement of labels should concern designers because it is all related to your brand. I searched through my stash to find examples of how other designers deal with US labeling requirements. I could not find any pieces that did not comply with labeling requirements. I guess I tend to buy product that is honest in their labeling. Clothing that leave off labels or fail to place them properly says something about your company (and it isn't good IMO). All of these examples have the labels correctly placed near the back neck with the country of origin prominently displayed.
Country of origin as part of the brand label. This is also one of my rare Made in USA pieces.
A size tag/country of origin label stitched to the bottom of the brand label.
A separate size/country of origin label placed next to the brand label.

This is a typical example. The brand label is stacked on top of the care/content tag. The country of origin clearly shows below the brand tag.




This is a typical example. The brand label is stacked on top of the care/content tag. The country of origin clearly shows below the brand tag.
Labels:
Analysis,
Care/Content Tags,
FTC,
Labels,
Regulations,
Technical Design
February 13, 2007
Another Care/Content Label Example

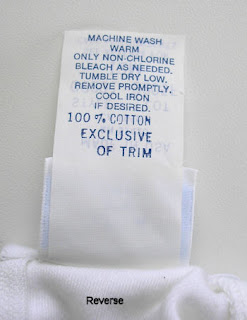
The first thing that caught my eye was the placement of the country of origin. Country of origin information must be placed so that it can be seen without flipping the label over. Nothing can cover the country of origin information, like a brand label. It should be placed in an easily accessible area, like the back neck or waistband.
Another interesting observation is the style number and lot number information included on the front of the label. The lot number probably refers to the production lot and corresponds to a date of manufacture (lot numbers are unique to each company, so it could mean almost anything). Generally, this information is found elsewhere, like the reverse of the tag or even on a separate tag stuck into a side seam. It is certainly not anything that a customer is going to care about. I like the inclusion of this info for easy back-tracking, but it should be placed elsewhere.
This tag contains both an RN and CA numbers. The CA number is the Canadian equivalent to the the US RN number. This product was most likely sold in both Canada and the US, thus the need for two numbers.
The reverse side of the label contains all relevant information. My only nit-pick is the overall formatting. I generally prefer the content information first, followed by the care info. This label is just the opposite. Further, the content information is a different font, font size, and right-aligned compared to the care instructions. It makes the whole reverse side appear sloppy.
My final nit-pick is that the label should say "2 piece set" somewhere. Inevitably, the two pieces will be separated. This helps the shipping and store employees on the retail end realize there should be two pieces on the hanger.
Labels:
Analysis,
Care/Content Tags,
FTC,
Labels,
Regulations,
Technical Design,
Tracking
Subscribe to:
Posts (Atom)