I seem to be a woman obsessed with blouses. Ever since I set out to create a basic blouse pattern for myself, I've kept my eyes open to study many RTW blouses. I've made many purchases from the thrift store with varying types of details and construction. I purchased this blouse a few months ago. As it usually goes, there were many things I liked about this blouse while I tried it on in the fitting room but I did note it was a little too big.

The refashion part of this post is probably the least interesting and so I don't have any before photos. I pulled out my basic blouse pattern and measured across the back at the base of the armholes. I compared that measurement with the blouse and did some math. The blouse needed to come in 1.5 inches on each side seam. Hmmm. The blouse was much bigger than I realized and made me recognize that our perceptions of body shape and size are definitely skewed when in a store fitting room. Anyway, the sleeves are set in flat so I just sewed up each side, taking it in the needed amount.

As I worked on the alterations, I took some construction notes. The front button band is a cut 2 (or 4, 2 for each side). A ruffle is gathered to the band that faces out on the long inner edge. The bands are sewn together on the outside edge and then stitched to the front bodice on the reverse side. The band is then turned to the front and topstitched down. I suspect the ruffle is not pressed down prior to topstitching. I think the operator used the ruffle to pull the band flat, turning the seam allowance to the inside. There is probably some interfacing on the band piece with the ruffle. The whole operation leads to a neat, clean finished button band. The operator who made this is probably very skilled, especially with dealing the bias area near the neck band. Still, this process is easier than it looks.
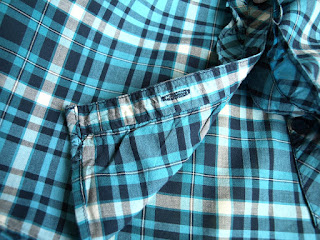
The only problem with this style is the ruffle. Despite a good ironing with some starch, the ruffle wants to stand up and fall over the buttons. The blouse is still cute, but perhaps a narrower ruffle would solve that problem?
While the sleeves were set in flat, the sleeve cuff was set in the round. The cuff was attached from the reverse side and turned out and topstitched down. I don't believe there was any pre-pressing because you can see the operator used a stripe of the fabric as a guide to turn the seam allowances in. If I were making this, I probably would pre-press just because I don't have the practice. The collar neckband was constructed in the same manner.